
By Mike Bumbeck
Photos by Mike Bumbeck and
RPS Performance Products
9/29/05
eat
is the sworn enemy of the clutch out on the 1320. Friction
created by the engagement of the clutch disc material to the
flywheel friction surface and pressure plate releases heat
as it transitions the energy of the engine into ground pounding
power. Too much power for the clutch setup, and the clutch
will start to slip and create more heat. More heat will cause
the clutch disk material to lose efficiency and slip more
– creating even more heat.
Excessive heat can burn up the clutch and put everything
back on the trailer or on the tow hitch. Even worse, things
can get dangerous. Some early AA Fuel Dragster "slipper"
clutches created so much heat that they turned into white-hot
circular shrapnel, shearing the cars in half. Just ask "Big
Daddy" Don Garlits, who cooked up the design for his
rear engine dragster while in the hospital recovering from
a fiery clutch explosion that destroyed his dragster and nearly
destroyed him.
While clutch technology as it applies to drag racing has
come a long way, heat is still the enemy, and can bring a
world of frustration to the table whether you're rowing through
the gears on a bracket car or trying to figure out how to
get thousands of nitromethane induced horsepower down to the
ground without you or your clutch setup getting burned. Finding
the right combination of friction materials and clamping force
for consistent launches that won't turn the transmission into
an expensive rock tumbler is the goal.
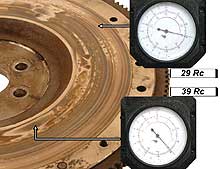
A factory Mustang flywheel shows
the difference in material hardness. Variances in can
remain even after the surface is machined flat, causing
corresponding difference in grip. This degree of overheating
can also result in flywheel shatter. |
SUPER FLY
Drag racing puts some heavy-duty demands on every component
of the clutch, but the flywheel takes the first and biggest
hit. Tremendous heat is generated on the friction surface
of the flywheel – especially if slipping the clutch
off the line is part of the race program.
Stock cast-iron flywheels are not only heavy, but can quickly
overheat, and are not rated to hold up to above stock RPM
demands. Think hot shrapnel again. A chromoly flywheel is
stronger and can therefore be made thinner and lighter, but
the steel surface is harder, which can lead to friction issues.
An aluminum flywheel with a steel heat shield friction surface
insert gets around these problems, but can create another.
The heat shield has nowhere to expand except against itself,
and can warp with extreme heat. This warping creates high
spots on the flywheel friction surface. This can cause slipping.
The slipping compounds the problem, as the heat created channels
through the high spots instead of being wicked away evenly
throughout the entire friction surface.
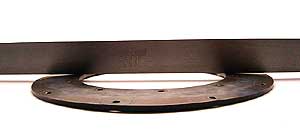 |
A used up heat shield
hoop from an aluminum flywheel shows the degree of warping
that can occur. Five to seven thousandths of an inch are
all it takes for a flywheel surface to start causing heat
and grip issues. |

|